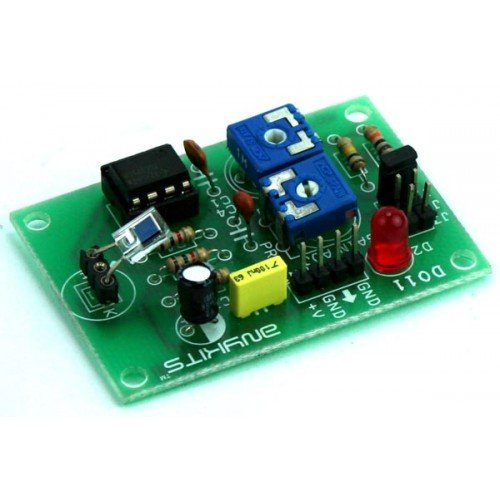
LUX METER MODULE
LUX Meter project has been design to measure the illumination. Illumination is luminous flux falling on surface area of photo diode. This illumination converted to corresponding voltage using Op-Amp circuit. SPECIFICATIONS Supply 9 VDC PP3 Battery @ 20 mA Onboard Photo Diode Onboard preset for calibration Range selection via jumper 10mV/LUX, 1mV/LUX, 0.1mV/LUX Interfacing is…